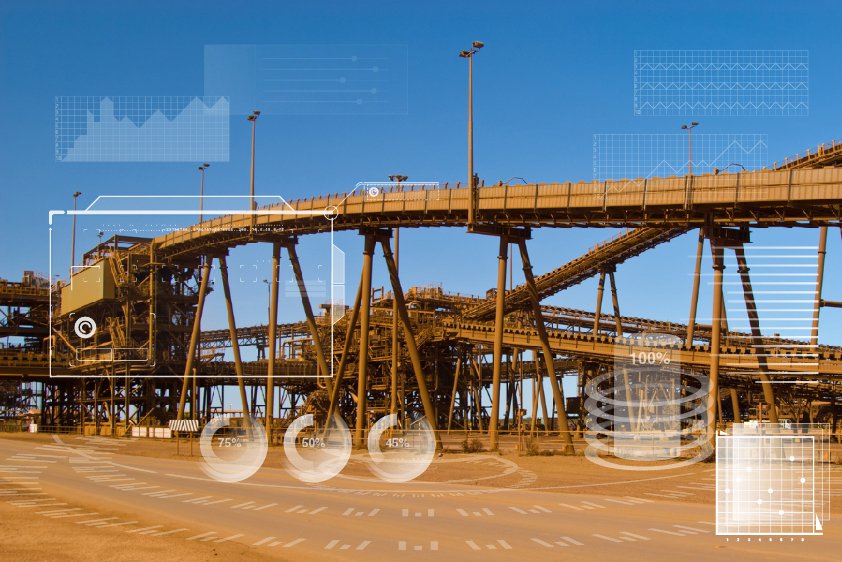
Identify & measure production bottlenecks in near real time
to prioritise work and improvements.
The Improvement Twin consists of a constraints model of your site value chains, and a tradeoff advisor to optimise initiative ROI or minimise production losses.
Optimising production requires collaboration and tradeoffs between multiple departments, across the site, across short and long time frames.
Process variability can't be avoided
Controls, work management and planning systems are aligned at the big picture level, but process variability often renders every plan sub-optimal in near real time. Managers are left to either follow the siloed but incorrect plan, or make it up as they go.
Prioritisation is difficult between silos
Prioritising changes and improvements is difficult without a global and visible measure of where the operational bottleneck is. Sometimes a fault or bottleneck in a local value chain has no impact on global performance, and can be safely ignored.
Direct cost is much easier than benefit, but not as valuable
Improvements should create more benefit than they cost, but sometimes we want to minimise production loss, and sometimes we want to maximise the ROI of the improvement. Without an agreed way of measuring benefit to production, it can be very difficult to decide what to do first and how much to spend.
The Geminum Improvement Twin highlights bottlenecks in near real time, measures cumulative production losses at the equipment and value chain level, and suggests which production losses should be improved to lift overall throughput.
Optimise Production with a Custom Constraint Model
We build a constraint model of your site or operation with you.
The constraint model consists of local value chains, which are the production units of your site. Starting with single chains and a historic batch of data to demonstrate and validate, we work up to every chain on site, and can extend to rail and port chains.
This is the fundamental data model of the Improvement Twin, that identifies bottlenecks in production.
Enhance Collaboration with Real-Time Production Visibility
With live production data connected, every team can see local bottlenecks as they appear, and cumulative production losses. When everyone can see and agree what the problems are in near real time, and how big the problem actually is over time, collaboration to mitigate the bottleneck is improved. Connecting additional data can improve fidelity and automated attribution.
Streamline and Track Improvement Initiatives
Improvement initiatives can be created with 1 click and improvement owners can access all historical production data associated with the value chain, and connected systems that may be impacted or contributing to the root cause.
Initiative owners can also see the progress of improvements (vs the ongoing cumulative production losses of the target system) and can recommend trade-offs to maximise ROI or minimise production losses.
Closed & rejected improvements are persistent to identify recurring issues and aid in strategic analysis of problems and actions.
Boost Maintenance Productivity with Predictive Insights
By extending the Improvement Twin to planning and maintenance systems, O&M teams can share near real time awareness of every emerging bottleneck across every value chain and re-prioritise work to take advantage of unplanned low production cost windows.
With predictive maintenance systems connected, the Improvement Twin allows maintenance and production teams to jointly decide when to take advantage of predicted but unplanned maintenance opportunities.
With a near real time and persistent view of bottlenecks across connected value chains, the Improvement Twin provides an excellent baseline for training and validating predictive models, and as an input to scenario planning and analysis exercises. As sites grow knowledge of the real process variations they encounter, increasingly sophisticated improvement initiatives and management controls will be possible. The ultimate vision of the Improvement Twin is to enable continuous improvement of integrated operations across all value chains.
Why Choose Our Digital Twin Specialists?
We are operations, cyber and data experts who have chosen to specialise in digital twins for asset intensive companies. We are not a body shop and we don't "build to spec".
We are the team that helps you develop, validate and deliver the roadmap and the products that you need to create truly integrated asset operations.